Descaling and Cleaning: Why High-Purity Phosphoric Acid Is Ideal for Industrial Maintenance
In industrial settings, equipment and piping systems are constantly exposed to water, steam and a variety of process chemicals. Over time, this exposure leads to the buildup of mineral scale - primarily composed of calcium, magnesium and iron compounds - as well as other types of residues and contaminants. Left untreated, these deposits can reduce operational efficiency, cause blockages, damage machinery, and ultimately increase maintenance costs and downtime. This is where industrial descaling and cleaning become essential parts of routine maintenance.
Descaling refers specifically to the removal of mineral scale, while cleaning more broadly covers the elimination of oils, rust, chemical residues and other contaminants. To achieve effective results, acids are commonly used due to their ability to dissolve or react with the unwanted deposits. Various acids like hydrochloric, sulfuric, citric and phosphoric acid are employed depending on the material compatibility, type of scale and environmental considerations.
Among these, high-purity phosphoric acid stands out as an optimal choice for many industries. Its unique chemical properties make it not only effective at breaking down scale but also safer, less corrosive and more versatile than many alternatives. In the sections that follow, we'll explore why high-purity phosphoric acid is a preferred solution for industrial maintenance applications.
What is High-Purity Phosphoric Acid?
Chemical Composition and Manufacturing Process
Phosphoric acid (H₃PO₄) is a mineral acid widely used in industrial, food and pharmaceutical applications. While technical-grade phosphoric acid contains a mixture of impurities and by-products from the manufacturing process, high-purity phosphoric acid is carefully refined to meet stringent quality and purity specifications.
The key difference lies in the degree of purification. High-purity grades are produced through advanced filtration, extraction and distillation processes that remove heavy metals, fluorides, chlorides and other trace contaminants. These refined products meet internationally recognized standards, such as FCC (Food Chemicals Codex), ACS (American Chemical Society), or E339 for food additives.
Typically, high-purity phosphoric acid contains 85% concentration with minimal levels of impurities, often below 1 ppm for critical elements. This high level of consistency and cleanliness ensures the acid is suitable for applications requiring maximum performance and minimal contamination risk — such as electronics manufacturing, pharmaceuticals, and high-end cleaning solutions.
Why Purity Matters in Industrial Applications
In industrial maintenance, the quality of cleaning agents directly affects both the effectiveness of the process and the longevity of equipment. Using lower-grade acids may introduce unwanted contaminants, including metal ions or organic residues, which can corrode metal surfaces, leave residues, or react unpredictably with other materials.
In contrast, high-purity phosphoric acid reduces the risk of contamination, ensuring safer application and more predictable results. It is also less aggressive toward sensitive surfaces, offering enhanced material compatibility and reduced corrosion, especially in stainless steel systems. The result is greater efficiency, longer equipment life, and better compliance with regulatory and quality standards across industries.
Key Industrial Applications of Phosphoric Acid in Maintenance
Scale Removal in Boilers, Heat Exchangers, and Pipelines
One of the most common maintenance challenges in industrial systems is the buildup of scale - solid mineral deposits primarily composed of calcium carbonate, magnesium salts and iron oxides. These deposits restrict flow, reduce heat transfer efficiency, and can lead to costly system failures. Phosphoric acid is highly effective at dissolving these mineral scales due to its ability to react with alkaline compounds, converting them into water-soluble salts that can be easily flushed out of the system.
High-purity phosphoric acid is especially beneficial in this context because it performs efficiently without introducing additional contaminants that could damage sensitive components or leave residual deposits. It is commonly used in boiler descaling, heat exchanger maintenance, and pipeline flushing in a range of industries, from power generation to chemical processing.
Rust and Corrosion Control
Phosphoric acid also plays a dual role in rust removal and corrosion prevention. When applied to steel and other ferrous metals, it reacts with iron oxides (rust) to form iron phosphate, a stable compound that can act as a protective layer. This process not only removes rust but also passivates the metal surface, slowing future corrosion.
Unlike more aggressive acids, high-purity phosphoric acid is gentler on the base material, making it an ideal choice for surface preparation before painting, coating or welding. Its controlled action ensures
effective cleaning without over-etching or weakening the structure of the metal.
Cleaning of Food-Grade and Pharmaceutical Equipment
In industries with strict hygiene and regulatory requirements, such as food processing and pharmaceutical production, the cleaning process must be both effective and safe. High-purity phosphoric acid meets these demands thanks to its non-toxic nature and compliance with food-grade standards like FCC and E339.
It is widely used to clean stainless steel tanks, pipes and mixing vessels, removing residues, biofilms, and scaling without compromising product safety. Because it leaves no harmful residues and does not introduce foreign contaminants, it supports both GMP compliance and product quality assurance, making it a trusted solution in sanitary maintenance protocols.
Benefits of Using High-Purity Phosphoric Acid Over Other Cleaning Agents
Compared to Hydrochloric Acid
Hydrochloric acid is a strong and commonly used descaling agent, but it comes with several drawbacks that limit its suitability for sensitive industrial applications. One major concern is its high corrosiveness, especially toward metals like stainless steel and aluminum. It can rapidly degrade equipment surfaces, leading to costly repairs or premature replacement.
In contrast, high-purity phosphoric acid is much gentler on metal surfaces, making it ideal for cleaning without compromising the integrity of machinery. It also produces far fewer harmful fumes, improving worker safety and reducing the need for intensive ventilation systems. For facilities seeking a balance between cleaning power and material compatibility, phosphoric acid provides a more controlled and less aggressive alternative.
Compared to Citric and Sulfamic Acids
Citric acid and sulfamic acid are often chosen for their lower toxicity and eco-friendliness, but they also come with limitations. Citric acid, while safe, is typically less effective at dissolving stubborn mineral scale, especially in high-deposit environments. It can also leave sticky residues that require additional rinsing. Sulfamic acid offers better performance, but its efficiency still falls short in comparison to phosphoric acid for certain applications.
High-purity phosphoric acid strikes a strong balance between cleaning strength and safety. It effectively dissolves scale and rust without excessive foaming or residue issues, offering an excellent cost-performance ratio in both industrial and hygienic environments.
Longevity and Preventive Maintenance Effects
One of the often-overlooked advantages of high-purity phosphoric acid is its contribution to preventive maintenance. Its ability to clean thoroughly without damaging surfaces means that equipment stays cleaner for longer periods, and the frequency of cleaning cycles is reduced.
Additionally, its passivating effects help form protective layers on metal surfaces, leading to lower wear and tear over time. This contributes to extended equipment life, fewer unplanned shutdowns, and overall improved operational reliability - key goals for any maintenance strategy.
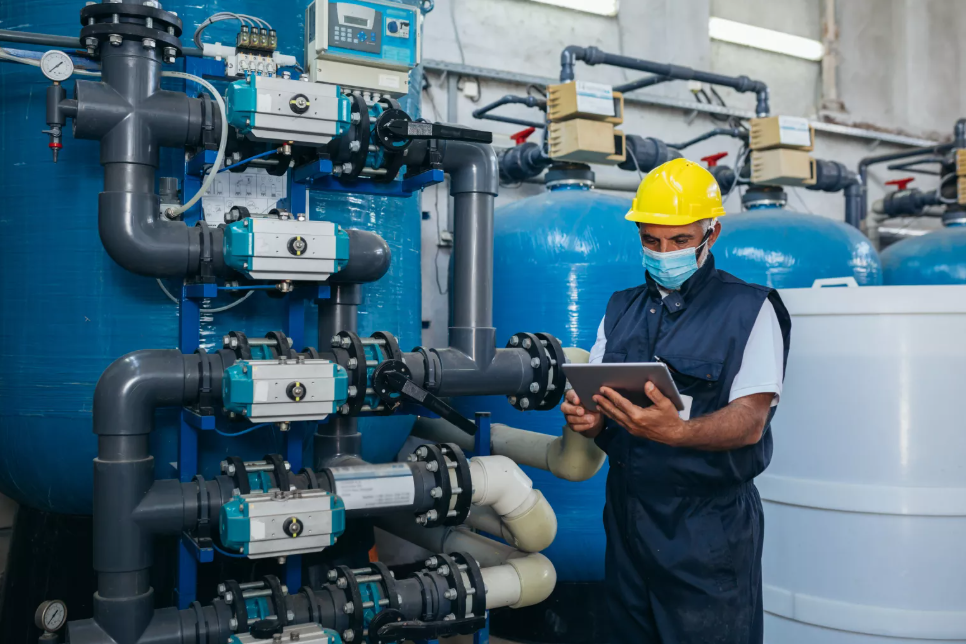
Safety, Handling, and Environmental Considerations
Personal Protective Equipment and Storage Guidelines
While high-purity phosphoric acid is considered safer than many alternative cleaning agents, it is still a corrosive substance that requires careful handling. According to standard Safety Data Sheets (SDS), personnel working with phosphoric acid should wear appropriate Personal Protective Equipment (PPE), including acid-resistant gloves, safety goggles or face shields, and protective clothing. In case of spills or splashes, immediate rinsing with water is critical to avoid irritation or injury.
Phosphoric acid should be stored in tightly sealed, corrosion-resistant containers, away from incompatible substances like strong oxidizers and bases. Storage areas should be well-ventilated and equipped with secondary containment measures to prevent accidental release. As with all industrial chemicals, staff should be trained on proper handling protocols and emergency response procedures.
Eco-Friendliness of High-Purity Phosphoric Acid
One of the key advantages of high-purity phosphoric acid is its relatively low environmental impact compared to more aggressive mineral acids. It is biodegradable in low concentrations and, when properly neutralized, is compatible with wastewater treatment systems. This makes it suitable for use in environmentally regulated industries, such as food processing and pharmaceuticals.
Unlike acids that introduce harmful heavy metals or toxic by-products into effluents, high-purity phosphoric acid ensures a cleaner discharge profile. However, proper waste management is still essential - neutralization with a suitable base (such as sodium hydroxide) and adherence to local
environmental disposal regulations help ensure responsible use and long-term sustainability.
Case Studies and Real-World Industrial Applications
Manufacturing Plants
In manufacturing environments, especially those involving high-temperature processes, heat exchangers are vital components that ensure efficient thermal energy transfer. Over time, these systems accumulate mineral scale, leading to reduced performance, increased energy consumption and eventual shutdowns for maintenance.
A European chemical manufacturing plant introduced high-purity phosphoric acid as a routine part of their heat exchanger maintenance. The results were significant: cleaning time was reduced by 30%, and the plant reported a noticeable improvement in thermal efficiency, leading to lower operational costs. Because high-purity phosphoric acid is less corrosive than hydrochloric acid, the plant also experienced less wear on stainless steel components, extending the lifespan of critical equipment.
Water Treatment Facilities
Water treatment facilities face a unique challenge: maintaining clean infrastructure while avoiding damage to sensitive equipment and coatings. Many facilities previously used hydrochloric or sulfamic acid for descaling, but encountered issues with corrosion and environmental discharge restrictions.
A municipal water treatment plant in Southeast Europe switched to high-purity phosphoric acid for descaling pumps and pipelines. The acid effectively removed scale without degrading pipe interiors or valve seals. Moreover, its compatibility with downstream wastewater treatment systems made disposal simpler and safer. Operators reported fewer equipment failures and extended cleaning intervals, highlighting phosphoric acid’s value as both a reactive and preventive solution in critical infrastructure.
These real-world examples demonstrate how high-purity phosphoric acid supports efficient, safe, and cost-effective industrial maintenance across sectors.
How to Source and Choose High-Quality Phosphoric Acid
When selecting phosphoric acid for industrial maintenance, purity and reliability are paramount. Not all products labeled as "phosphoric acid" meet the same standards, so it’s essential to evaluate suppliers carefully. Look for vendors who provide certifications such as FCC (Food Chemicals Codex), ACS (American Chemical Society), or REACH compliance, which indicate adherence to stringent quality and safety standards. Reputable suppliers will also offer Certificates of Analysis (CoA) and purity guarantees, detailing impurity levels and batch-specific data.
Beyond chemical purity, consider packaging and storage options. High-purity phosphoric acid is typically available in HDPE drums, IBC totes, or bulk containers, depending on your operational scale. Ensure that the packaging is corrosion-resistant and sealed to prevent contamination or moisture ingress during transport and storage.
Proper storage conditions are also critical. The acid should be stored in a cool, dry, and well-ventilated area, away from incompatible materials such as bases and oxidizers. Secondary containment is recommended to manage potential leaks safely.
Partnering with a trusted supplier, like DECACHEM, not only ensures product quality but also provides technical support, regulatory documentation, and consistent supply - all of which are crucial for maintaining operational efficiency and safety in industrial settings.
Frequently Asked Questions (FAQs)
What concentration of phosphoric acid is best for descaling?
For most industrial descaling applications, an 85% high-purity phosphoric acid solution is commonly used, often diluted to around 10–30% depending on the severity of scale and the equipment being cleaned. Always follow manufacturer or process-specific guidelines for optimal results.
Is phosphoric acid safe for stainless steel?
Yes. High-purity phosphoric acid is safe and compatible with stainless steel, especially when used at recommended concentrations. Unlike more aggressive acids such as hydrochloric acid, it minimizes corrosion and preserves the integrity of metal surfaces.
Can it be used in food-processing environments?
Absolutely. When sourced as FCC-grade or food-grade phosphoric acid, it meets the strict standards required for use in food and beverage production. It is commonly used to clean stainless steel tanks, pipelines, and process equipment in hygienic environments.
How often should descaling be performed?
The frequency depends on water quality, equipment usage, and system design. In general, preventive descaling every 6–12 months is recommended, or more frequently in high-deposit environments.
What are the signs that descaling is needed?
Indicators include reduced heat transfer efficiency, pressure drops, flow restrictions, increased energy usage, and visible scale buildup. Regular monitoring helps detect these issues early and avoid unplanned downtime.
Conclusion: Why High-Purity Matters for Effective Maintenance
High-purity phosphoric acid offers a powerful combination of effective scale removal, surface safety, regulatory compliance, and environmental compatibility. Compared to lower-purity or more aggressive acids, it provides superior performance with reduced risk to equipment and personnel. For industries seeking reliable, long-term maintenance solutions, upgrading to high-purity formulations is a smart investment.
DECACHEM supplies high-grade phosphoric acid tailored to industrial and hygienic applications, helping facilities enhance efficiency, extend equipment life, and meet the highest safety standards. Choose purity - choose performance.
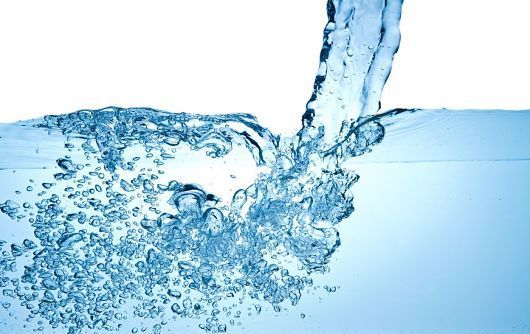
